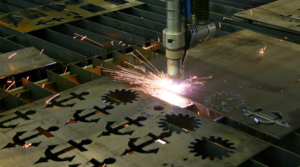
We have many customers who say they can’t afford to upgrade/retrofit their machines, they do not have enough time to do it either due to cost or downtime needed.
However if you’re running a pre or early PC based CNC, DC brushed drives, or any other older equipment, then you may be in for some lengthy unscheduled downtime due to the machine breaking often.
Let’s take the early Burny 2.5/3/5 series of CNC controls for instance. In their day they were the best out there. They were good, rugged, and the fastest thing you could get. With a whopping 4 MHz processor, and 1⁄2 Megabyte of memory, they cut lots of parts. Over the 15 plus years they were manufactured, there were thousands of them put in service. All the major Cutting Machine manufacturers used them on one machine or other. (Even ESAB)! Lots more were retrofitted on machines with early Bendix and A-B CNC’s. What happens when they break down?
There are no longer any new parts for them. Some of the IC chips are no longer manufactured, and a few of the IC companies have gone out of business. CMC/Burny has been sold a few times, and no longer have parts, or sometimes even Service Techs who know the old stuff.
You can look on the internet/E-Bay for used systems/parts, and hope they work. Over the years Burny designed newer boards, and they are not compatible with the older systems. You need to make sure you are matching the board numbers when scouring for parts.
And when you get it running again, you still have the same old system. You have bought time and not reliability. The Burny drives and early Burny 10 and 10LCD controls are the same. They stopped making parts available.
This problem is not unique to burny it is also true with early Centricut/Hypertherm Automation, ESAB, MG, Koike, Westinghouse/Creonics units.
The older Hypertherm, Innerlogic & Thermal Dynamics Plasma Systems and Torch Height Controls are also obsolete, and unsupported.
When they do go down, they can have as devastating an effect on productivity and often mean you have to outsource this part of your production line which is costly.
Typically it takes 6-8 weeks to prepare and deliver a machine retrofit. Most of the parts have a 2-4 week lead time, and they have to be integrated into a system and our production schedule.
When considering on updating your aging cutting machine think about what it costs to have your machine go down for unscheduled downtime due to aging parts braking. Don’t think of the retrofit cost, but lost production time. Depending on your special set of circumstances, it could cost more in money and lost customers than the retrofit would cost, if it was planned ahead of time.
We have lots of customers who have gotten quotes 2 to 3 times over a few years, and done nothing, said it was too expensive, or the system is working fine. When their machine goes down its big issue.
Depending on our schedule we, or our installers, can sometimes get on site in 3-4 weeks. We choreograph this so your machine (if its still running comes offline when we are there to do the retrofit.) This helps reduce the downtime needed for the retrofit installation.
Buy a new machine is an option but most manufacturers are looking at least 16-20 weeks out on delivery with a few more weeks to install… New machines are generally more than double the cost of a retrofit.
Give us a call and we can plan this for a more convenient time, when it does not double the cost.